February 20, 2017
Why Is Hands-On Training Important?
Video tutorials aren't quite the same.
In the age of YouTube videos and webinars, embroidery educators make the case for in-person learning.
Joyce Jagger, The Embroidery Coach:New embroiderers should include hands-on training in their startup budget. It’ll help them see a return on investment much quicker than trying to learn how to do it all on their own. Because there are many variables in the process, building a good foundation greatly reduces mistakes and lowers the learning curve. Some of the biggest mistakes new embroiderers make are in placement, hooping and what types of backing to use. Often, these mistakes ruin a costly garment. While there’s a lot of information on the internet, it’s not always reliable. It’s better to invest in training from a seasoned expert who can give you hands-on help.
In addition to offering on-site consulting and training, I’ve opened a training center in my home to teach the process of embroidery step by step, and how to set up the proper systems to run your business. Learn more at PersonalizedEmbroideryTraining.com.
Justin Schierkolk, Melco International: Even the simplest embroidery machines require the use of your hands to operate them. Installing and orienting needles, threading the machine, installing and changing bobbins, adjusting bobbin and thread tension and controlling machine functions through a keypad or interface are just a few areas that require physical interaction with the machine. Hooping is also a learned skill that requires hands-on practice to master. First-time users benefit greatly and learn much faster by getting in front of a machine with a certified trainer. Instant feedback from a pro on things you’re doing right or need to adjust has a huge impact on the time it takes to become an expert.
Melco provides onsite training as part of buyers’ equipment package, and offers classroom training at Melco headquarters, centrally located in the U.S., just north of Denver.
Bill Garvin, BG Tech Services: Nowadays, it’s easy to do webinars, YouTube videos and even FaceTime to learn about the industry and how to operate equipment. But relying on those methods alone is like trying to become a great driver simply by playing video games. Hands-on classroom experience will always be the best for learning and memory retention. See, learn and do – all under the watchful eye of a professional who’s been there and done that. Learning the basics of machine operation, speed and maintenance, as well as hooping techniques, will be your best defense against issues with your machine.
I opened the Embroidery Training Center (ETC) in St. Petersburg, FL, to help embroiderers do more with their equipment. I love passing on the experiences I’ve learned over the last quarter century. (Check out my calendar of events at www.bgtechservices.net.)
Henry Ma, Ricoma:Embroidery is learned best through one-on-one time with an expert. While the web is useful for tips, first-timers or those who want to improve their embroidery skills should receive live, hands-on training with a product specialist. The reason is simple: Embroidery is a visual craft, and the key is in the details. You might think a design turned out fine, but a pair of trained eyes can catch your small errors. The upshot: A lot of details can be captured in person, and those specifics can set you apart from the competition. Hands-on training allows you to learn correctly from the beginning, helping to prevent bad habits from developing.
We offer training at our Miami headquarters. Customers are welcome to attend in groups or bring family or friends. We go through a structured curriculum that covers everything from the basics to maintenance. Customers who buy multi-head machines receive two full days of free on-site training.
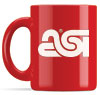
Product Hub
Find the latest in quality products, must-know trends and fresh ideas for upcoming end-buyer campaigns.