March 22, 2018
How Screen Printers Can Effectively Use White Ink
White plastisol ink tends to give screen printers trouble, but we have the cure.
White ink, used as an underbase and as a highlight to other colors on dark shirts, tends to give screen printers a lot of trouble. A full 99 of every 100 calls I receive about printing issues will, in one way or another, come back to printing white ink on dark garments. A lot of printers want to know which white ink is best to use. The type of white ink isn’t what’s important; instead, it’s all about how you use it.
Opaque white plastisol ink is specifically formulated to offer a crisp, clean, white print on dark 100% cotton garments. The 100% cotton factor is important. This version of white ink is produced without the required chemistry to resist bleeding of fabric dye into the printed ink film. Bleeding of color into the ink film, known as dye migration, is a function of cotton/poly blends or 100% polyester and not common with 100% cotton garments.
Low-bleed white is specifically formulated to be used on dark cotton/poly blend garments. This ink must first be opaque enough to hide the garment color, and second, have the proper chemistry to resist dye migration from the polyester portion of the garment makeup. Bear in mind, these inks are only called low-bleed and bleed-resistant. No ink on the market today can completely block all dye migration.
It’s important to use a white underbase and a separate highlight white if there is white in the image. Courtesy Oklahoma Shirt Company.
Avoid dye migration: Dye migration is the result of dye in polyester fibers sublimating through the ink film. The dye from the cotton portion of fabric won’t migrate. If you print any blend fabrics – cotton and polyester – you’re at risk of dye migration. Most commonly, this effect occurs in red, Kelly green and maroon, but it can be a risk with other blend colors as well.
The most common factor affecting dye migration is excessive heat. Many screen printers operate their conveyor dryers at much higher temperatures than necessary to cure plastisol inks. This goes unnoticed until blended fabrics enter the mix. Heat causes the dye to release from the polyester fibers. More heat equals accelerated release. Testing for full curing temperature without substantially exceeding that temperature will minimize dye migration.
Another tip to help minimize dye migration: Don’t allow blend garments to fall into a box or catch basket at the end of the dryer belt. Before stacking, shake garments to cool. Heat from hot-stacked garments can draw dye from the garment on top into the ink on the garment below.
Create a white underbase properly: The most common mistake with creating a white underbase is in using the white of that underbase as the white in the image. In other words, if there’s white in the image, a second highlight white should always be used, rather than the white of the underbase. If the underbase is used, you’ll lay down far too much ink to make it bright enough for the image. A thin underbase that’s not necessarily bright white is all you need, then a highlight white will give you a much thinner and more crisp finished product.
Use the proper mesh: Common mistake number two is using too low a mesh count for white. If this much white is good, more must be better, right? That’s incorrect. It’s rare that I would ever use any mesh lower than 156 to create an underbase. With simulated process, I regularly use a 230 mesh and achieve a brilliant bright image. If you’re using 110 mesh because your dealer suggested it, you’re laying down far too much white ink.
Dealing with thick ink: White ink can be difficult to work with due to its thickness, especially if your shop is cool at night. The quick solution is to scoop out what you need for your job and just stir it up. It should loosen and print much easier after stirring.
White ink is the most talked about and debated product on the production floor. But remember, it’s not the ink that’s the issue, it’s how you use it that matters.
***
Terry Combs is a 35-plus-year veteran of the garment-printing industry and has managed production shops across the United States. He is currently in sales and training with Equipment Zone, Franklin Lakes, NJ, working from Scottsdale, AZ.
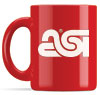
Product Hub
Find the latest in quality products, must-know trends and fresh ideas for upcoming end-buyer campaigns.